キーワード:全固体電池/長寿命/省資源
近年、リチウムイオン電池に代わる電池として期待されている「全固体電池」。過充電や加熱などによる発火の危険性がなく、過酷な環境下でも長期間使用できる電池として注目を浴びています。EV向けなどの大型の電池は開発途上にありますが、実は世界に先駆けて小型全固体電池の量産化に成功した企業があります。1961年の創業以来、「まぜる」「ぬる」「かためる」アナログコア技術を強みにさまざまな電池を作り続けてきたマクセル株式会社です。同社は2018年頃からリチウムイオン電池に代わる新たな電池の開発に本格着手し、2023年に世界で初めて小型硫化物系全固体電池の量産を開始しました。開発当初からプロジェクトに携わってきた山田さん、古川さん、佐藤さんにお話をうかがいました。
Person
マクセル株式会社 新事業統括本部 担当本部長
山田 將之
1996年入社。マクセルでのリチウムイオン電池開発が始まった時に研究所に異動。2009年、自身が開発した材料がサムスンのスマートフォンに採用されたのを機に、電池事業を手掛けるエナジー事業本部へ。以降10年間スマートフォン向けリチウムイオン電池の開発に従事。2019年からリチウムイオン電池に替わる新電池の開発に携わる。現在は、全固体電池全般の統括リーダーを担う。
Person
マクセル株式会社 新事業統括本部 製品開発部 材料科 技師
古川 一揮
日本初、世界初の製品開発にチャレンジするマクセルの企業姿勢に惹かれ、2015年に入社。ドローン用の高出力リチウムイオン電池や医療用長寿命リチウムイオン電池の開発に取り組んだ後、2018年から初期メンバーとして世界初のセラミックパッケージ型全固体電池の開発に携わる。
Person
マクセル株式会社 新事業統括本部 ビジネス開発部 企画課
佐藤 優太
大学時代から全固体電池を扱う研究室に所属しており、2018年の入社後も全固体電池の開発に従事。自身の専攻が活かせるというだけでなく、マクセルのチャレンジ精神から「裁量が大きく個人が成長しやすい環境」と考え、同社を志望した。
自社の強みを生かし、マイクロ電池に革命を起こす
――全固体電池の開発にマクセルが取り組むことになった経緯を教えてください。
山田:リチウムイオン電池は充電可能な二次電池として非常に優れていますが、過充電や加熱による発火などの課題は皆さんご存知のことだと思います。そのため、多軸ロボットの関節部分など過酷な環境で使われるセンサーの場合、従来のリチウムイオン電池では安全面で対応できません。加えて、これまでのような電子機器だけでなく、あらゆるところにセンサーが普及し、そこに電力を供給する電池が必要になるなど、求められる電池の数や種類も増えています。
このように既存の電池ではどうしてもカバーしきれない要求が増えてきたため、当社も安全でさまざまな用途に使える新たな電池の開発に着手しました。全固体電池以外にも、今も開発中の水溶液系二次電池、人体や環境に無害な物質で構成された捨てられる電池など、いろいろな電池に挑戦しましたが、今一番可能性が大きくなっているのが全固体電池です。
――改めて、全固体電池の特長を教えてください。
佐藤:全固体電池は、電解質が従来のリチウムイオン電池のような液体ではなく、固体で構成されている電池です。発火の危険性がある電解液を使わないことによって安全性が担保され、低温下で凍ってしまい機能しなくなることもありません。また、固体は化学的に安定しているので劣化しにくく、リチウムイオン電池よりもさらに寿命を延ばすことができるほか、温度変化や圧力変化に強く、さまざまな環境下で安定して動作します。
――どれくらい過酷な環境で使えるのですか。
古川: 普通のリチウムイオン電池は電解質に液体を使っており、その沸点が80℃程度のため、100℃以上の高温下で使用することは困難です。一方、固体電解質であれば、数百度でも安定しているのでかなり広範囲の用途で使うことができます。特にマクセルの全固体電池は、お客様からも「耐熱・長寿命特性で右に出るものはない」という嬉しい評価をいただいています。2024年には作動上限温度を 150℃に引き上げる技術開発にも成功しました。
――それであれば用途が格段に広がりそうですね。2018年から本格的に開発を開始されていますが、マクセルさんは比較的早く、全固体に目を付けられていたのでしょうか?
古川:すでに取り組んでいた会社もありましたが、小型かつ耐熱長寿命の硫化物系全固体電池に着目しているのは当社だけでした。実は、そこが差別化のポイントになっています。つまり、「他社にない技術を持っている」ということ。当社は一般的な角形のリチウムイオン電池だけでなく、小型のコイン形リチウムイオン二次電池など、さまざまな電池の技術がベースとしてあり、そこで培った「アナログコア技術」が生きています。
山田:当初は、スマートフォンやパソコン、モバイルバッテリーなどに使われる比較的大きな電池をイメージしていましたが、微小な電子機器や医療機器、ウェアラブルデバイスなどに使われるコイン形電池などのマイクロ電池を作っているエナジー事業本部と連携することになり、「まずはマイクロ電池で全固体電池を作ろう」という方向になりました。ちょうどマクセルのコイン形電池も耐熱性・長寿命性を追求していたことに加えて、環境面への配慮から使い捨ての小型一次電池を二次電池化していく流れがあったので、非常にタイムリーでした。
とはいえ、しばらく手探り状態が続きました。例えば、全固体電池は粉末を押し固めて作るのですが、最初はどれくらい押し固めたらよいのか、どれくらいの厚みがよいのか、どの材料が適しているか、などが分からず、全くうまくいきませんでした。そこからトライ&エラーを繰り返すうちに「ある所まで圧縮すると特性が出る」ということがだんだんわかってきて、厚みと密度、詰め込み方、空隙をどれだけ減らすかが分かったところから急激に開発が進みました。
佐藤:また、全固体電池に特化した材料も開発する必要がありました。そこで、交流のあるサプライヤーさんと協業しながら進めました。こうしてプロセスも、材料もカスタマイズしながら最適解を導き出せた結果、コイン形全固体電池ができたのです。
コイン形全固体電池
常識を覆す製品で客先の工程削減にも貢献し普及を促進
――2021年にセラミックパッケージ型の全固体電池を開発されました。こちらはどんな特徴がありますか。
古川:セラミックパッケージ型全固体電池は、電池では前例がない外装体にセラミックを採用したマイクロ電池です。この特徴の一つは実装性で、耐熱性という全固体電池の特徴を活かし、基板上に他の電子部品と一緒に置いてリフロー炉という高温の炉で一気にはんだ付けすることができます。
通常の電池は後から端子を付けて基板に接着、通電するのですが、この電池であれば電子部品と同じように取り扱うことができ、すぐに電源としてお使いいただける画期的な製品です。
山田:リフロー炉というのは245℃付近の熱を持っています。普通の電池では破裂する温度ですから、全固体だからこその製品と言えますね。
セラミックパッケージ型
評価用電源モジュールキット
――確かに、お客様先の工程も大幅に効率化できますね。開発にはどのようなブレイクスルーがありましたか。
古川:全固体電池は水分に弱く、通常のスマートフォンに入っているリチウムイオン電池のようにラミネート型のままでは十分に対策できていませんでした。そこを解決してくれたのが耐水性、封止性の高いセラミックパッケージです。電池をセラミックパッケージで出すというのはかなり画期的なアイデア、技術が投入されています。
山田:その前にコイン形全固体電池の開発で成果を得ていたからこそ、いち早く課題に気づくことができて、セラミックパッケージにつながりました。
一般的にはラミネート型で開発しているため、特性が悪かったとしても「中身」や「作り方」が悪いと思いがちです。しかし、すでにコイン形の開発で中身が安定していることはわかっていたので、ほかの原因があることが分かっており、すぐに「外側を変えればいいのでは」というアイデアに思い至りました。こうした方法はあまり知られていなかったと思います。
――全固体電池へのお客様の反応はいかがでしょうか。
佐藤:私はお客様の技術窓口も担当していて、お客様の困りごとやニーズを把握し、それを開発に活かすことがミッションです。
採用を検討いただくお客様からは、非常に良い反応をいただいています。メンテナンスフリーなどお客様の解決したい社会課題にベクトルを合わせることを心掛けて、それを一緒に解決するビジネスパートナーとして密に連携するようにしています。
電池の“永久電源化”で使い捨てではないサステナブルな社会へ
――今後は他にどんな用途を考えていますか。
古川:今は、我々が主に取り扱っているのが小型の全固体電池ですが、さらにそれを大きくした、スマートフォンなどに使えるようなサイズの新しい全固体電池を開発しています。
2023年にはセラミックパッケージ型の25倍の容量がある円筒形の全固体電池を開発しました。主な市場として想定している産業分野では円筒形の電池が使われることが多いので、同じ形状にすることでお客様に受け入れられやすくしています。さらに、サイズアップを図るとともに今の125℃からもっと耐熱性能を上げ、特殊インフラ用途でも使用できるようなタイプを開発中です。
円筒形全固体電池
山田:これまでの既存電池では対応できなかった所にどんどん使っていただききたいですね。一般環境で使えば5年くらい使える電池を1か月ごとに交換しながら動かしている過酷な環境の現場もたくさんあるはずで、不満をもっているお客様がたくさんいるはずです。そこを全固体電池に置き換えていただきたいと思いますし、環境や資源保全の面でも有効な製品を開発していきたいです。
古川:特に百数十度で安全に使える電池は少なく、我々の全固体電池であれば安心・安全に使っていただけます。それを大切にしながら、さらに長寿命化でお客様のメンテナンス回数を減らし、労働力不足などの社会課題にも貢献するというのが一つの大きな目標です。
セラミックパッケージ型全固体電池に関しては、2023年にロームグループとの協業でエナジーハーベスト対応のモジュールキットを開発しました。このような仕組みを活用すれば、太陽光や室内照明からの発電による完全メンテナンスフリーの電池が実現します。ファクトリーオートメーションやインフラ分野のモニタリング、表示デバイスに活用していくことができればと考えています。
ソーラー発電パネル(左)とエナジーハーベスト対応評価用低消費電流モジュールキット(右)
ソーラー発電パネル提供: 株式会社リコー
――まさに「永久電源」ですね!コイン形は、冒頭で医療向けやウェアラブル端末という話がありましたが、他にも用途がありますか。
佐藤:インプラント用にも活用が見込まれます。電解液系の電池では液漏れのリスクがありますが、全固体電池はその心配がなく、かつ長寿命のため医療用途にも適しています。
古川:私は以前医療用の長寿命リチウムイオン電池開発に携わっていました。電解液は引火性の物質になってしまうのですが、全固体電池は基本的には難燃性物質しか使われていないので、安全性の面で医療と親和性が高いですね。
――このプロジェクトの魅力や社会課題解決に貢献している手応え、仕事の醍醐味を教えてください。
山田:今、全固体電池をいろいろなところでリリースしていますが、とくに産業機器や車載用途で非常にたくさんの問い合わせをいただいています。お客様ご自身が環境や社会課題を解決したいという想いを持たれており、我々だけではなく、社会全体でSDGsなどの達成に大きな関心があるということを感じます。
また、今まではスマートフォン用の電池は2~3年という短いサイクルで商品が入れ替わるため、容量が大きいことや一度の充電で長時間使えることが求められ、長寿命という観点での相談はあまりありませんでした。しかし、ヨーロッパでは乾電池など使い捨ての電池はダメという認識が広がりつつありますし、充電して繰り返し長く使える二次電池へのニーズがますます大きくなっています。それを達成するには全固体電池がベストなソリューションだと思います。
佐藤:私はエネルギー・環境問題にはもともと興味があり、大学で全固体電池を扱う研究室に入りました。今はどこを見ても電池が必要で、特に今後は二次電池が重要になると考えたからです。その後マクセルに入社して、日々新しい製品開発にチャレンジできることに未だにワクワクしています。その分、タスクが多く大変なこともありますが、「若い時の苦労は買ってでもせよ」という言葉を胸に、これからも世の中の課題を解決するような製品開発に携わっていきたいと思います。
取材後記
以前からマクセル様の全固体電池について知ってはいましたが、小型に特化した戦略や開発の裏話をうかがうことができて、改めてそのすごさを実感しました。
普段あまり目にすることはありませんが、小型電池は産業を支える縁の下の力持ちのような存在で、それがこの全固体電池に置き換われば環境や社会に与える影響は非常に大きいと思います。
同社は2030年までに売上規模300億円という目標を掲げており、今後の普及促進に期待しています!
(ブレーンセンターAN)
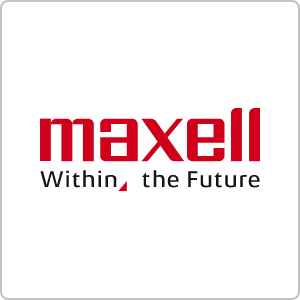
祖業である電池事業と、電池事業で培った「まぜる」「ぬる」「かためる」アナログコア技術を活用し、建築・建材用や半導体製造工程用などのテープを扱う機能性部材料、車載カメラ用レンズやヘッドランプレンズなどの光学部品を扱う光学・システム事業を展開。リチウムイオン電池に代わる次世代電池として期待される全固体電池は量産を開始しており、2030年に300億円規模の売上を目指して普及に努めている。